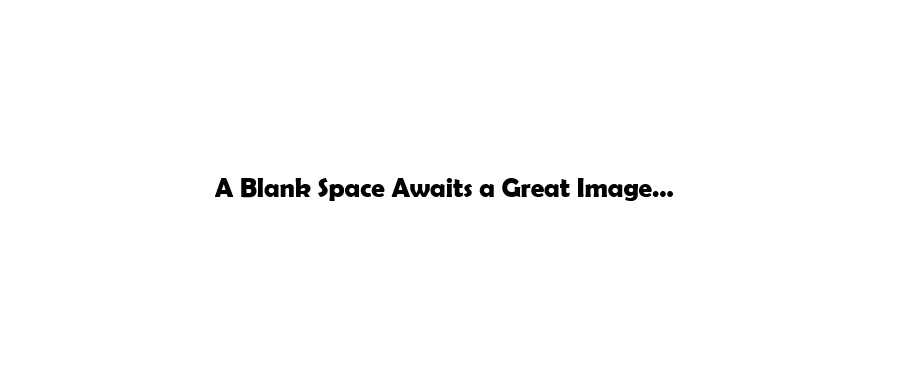
Introduction to PWHT and Crack Prevention:
Post Weld Heat Treatment (PWHT) is a critical process used to enhance the structural integrity of welded metals. One of its most significant advantages is its ability to prevent cracks in metal components, ensuring durability and safety in industrial applications. At PWHT Tech India, we provide state-of-the-art PWHT solutions that eliminate residual stresses, refine microstructures, and prevent various types of cracking in welded materials.
Why Do Cracks Form in Welded Metals?
Cracks in welded metals occur due to multiple factors, including thermal stresses, material properties, and environmental conditions. The most common types of cracking in welded structures include:
✔ Residual Stress Cracking – Occurs due to uneven heating and cooling during welding, leading to internal stresses. ✔ Hydrogen-Induced Cracking (HIC) – Hydrogen atoms trapped in the weld cause embrittlement and crack formation. ✔ Stress Corrosion Cracking (SCC) – Happens when tensile stresses combine with corrosive environments. ✔ Hot Cracking – Develops when liquid metal solidifies too quickly, creating internal fractures. ✔ Cold Cracking – Results from delayed cracking due to residual stresses and hydrogen absorption. ✔ Fatigue Cracking – Occurs due to cyclic loading over time, leading to gradual fracture.
How PWHT Prevents Cracking in Metals?
Post Weld Heat Treatment (PWHT) is designed to minimize residual stresses, refine the microstructure, and improve mechanical properties, effectively preventing crack formation in metals. Here’s how PWHT helps:
1. Reduction of Residual Stresses
Welding generates high internal stresses due to rapid heating and cooling cycles.
PWHT gradually relieves these stresses by heating the material to a controlled temperature and allowing slow cooling.
This stress relief prevents sudden crack initiation under mechanical loads.
2. Hydrogen Diffusion and Elimination
Hydrogen-induced cracking (HIC) is a major problem in high-strength and alloyed steels.
PWHT at the correct temperature allows hydrogen to diffuse out of the metal, reducing brittleness and cracking risk.
Common temperature ranges for hydrogen diffusion are 250°C – 400°C, depending on the material type.
3. Microstructure Refinement
Rapid cooling during welding can create hard and brittle microstructures, increasing crack susceptibility.
PWHT transforms unstable microstructures into ductile and tough phases, improving material strength and toughness.
This is especially important for high-carbon steels and alloy steels, which require controlled heat treatment.
4. Improved Toughness and Ductility
Hard and brittle welds are more prone to cracking under stress.
PWHT enhances the toughness and flexibility of the weld, making it more resistant to external forces.
It ensures better performance under mechanical loads, thermal expansion, and vibration.
5. Prevention of Stress Corrosion Cracking (SCC)
SCC occurs in environments with high humidity, chemicals, or saltwater exposure.
PWHT reduces internal stresses, making the metal less susceptible to crack propagation due to corrosion.
This is vital for industries such as oil & gas, marine, and chemical processing.
6. Control of Hardness in Heat-Affected Zones (HAZ)
The Heat-Affected Zone (HAZ) in a weld is prone to excessive hardness and brittleness, leading to cracking.
PWHT reduces hardness and equalizes mechanical properties across the weld and base metal, preventing failures.
PWHT Techniques for Crack Prevention
Different PWHT techniques are used based on material type and industrial applications:
1. Furnace Heat Treatment
Suitable for large pressure vessels, boilers, and structural components.
Provides uniform heating to prevent crack formation in critical areas.
2. Localized PWHT (Resistance Heating)
Used for pipelines, storage tanks, and field-installed structures.
Targets specific welded joints to relieve stress and prevent localized cracking.
3. Induction Heating PWHT
Rapid and controlled heating using electromagnetic induction.
Ideal for offshore, refinery, and pipeline applications.
4. Oil & Gas Firing PWHT (FireWave System)
Utilizes high-efficiency oil and gas burners for large components.
Used in storage tanks, pressure vessels, and offshore projects.
5. On-Site and Mobile PWHT
Designed for remote locations and large industrial projects.
Brings advanced heat treatment technology directly to the worksite, ensuring minimal downtime.
Industries That Rely on PWHT for Crack Prevention
✔ Oil & Gas – Prevents cracking in pipelines, pressure vessels, and refinery equipment.
✔ Power Plants – Ensures durability of boilers, steam turbines, and high-pressure piping.
✔ Petrochemicals & Refineries – Reduces cracking risk in heat exchangers and storage tanks.
✔ Marine & Offshore – Enhances the strength of ship hulls, offshore platforms, and underwater structures.
✔ Aerospace & Heavy Engineering – Strengthens high-performance alloys in aircraft and machinery.
PWHT Tech India – Your Trusted Partner in Crack Prevention
At PWHT Tech India, we provide expert PWHT solutions that ensure weld quality, structural integrity, and compliance with ASME, API, ISO, AWS, and EN standards.
✅ Cutting-edge PWHT furnaces and mobile on-site solutions.
✅ Highly skilled engineers and certified heat treatment specialists.
✅ Comprehensive stress analysis and quality assurance reports.
✅ Custom heat treatment solutions for various industries.
With our advanced PWHT technology and expertise, we help industries prevent metal cracking and structural failures, ensuring long-term reliability and safety.
Conclusion
Crack prevention in welded metals is crucial for safety, durability, and regulatory compliance. Post Weld Heat Treatment (PWHT) plays a vital role in reducing residual stresses, improving microstructure, and enhancing mechanical properties to prevent various types of cracking.
PWHT Tech India is your trusted partner for world-class PWHT solutions, ensuring crack-free and high-performance welded structures.
For expert PWHT services, contact PWHT Tech India today!