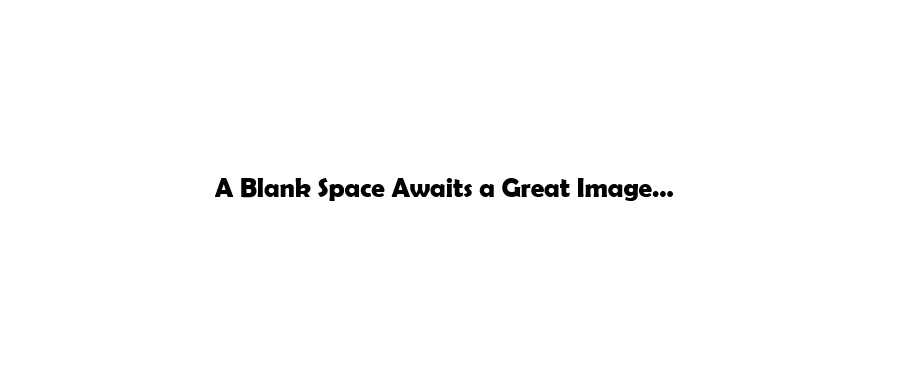
Introduction
Post Weld Heat Treatment (PWHT) is a crucial process in industries dealing with high-pressure components such as pressure vessels, pipelines, and steam boilers. The primary function of PWHT is to reduce residual stresses, improve mechanical properties, and enhance the overall integrity of welded structures. However, some industry professionals explore the possibility of avoiding PWHT to reduce costs and processing time. This article evaluates whether avoiding PWHT is feasible and under what conditions it might be acceptable according to international standards.
Understanding the Role of PWHT in High-Pressure Components
High-pressure components are subjected to extreme operational stresses, which can lead to issues such as:
- Residual welding stresses
- Hydrogen-induced cracking
- Brittle fracture
- Stress corrosion cracking (SCC)
- Reduced toughness in the heat-affected zone (HAZ)
PWHT is designed to mitigate these risks by relieving internal stresses, refining the microstructure, and enhancing ductility. Omitting PWHT requires careful evaluation of alternative methods that can achieve similar benefits.
Conditions Under Which PWHT May Be Avoided
While PWHT is generally recommended for high-pressure components, there are certain cases where it may be omitted or replaced by alternative treatments. The decision depends on material selection, welding techniques, operating conditions, and compliance with industry standards.
1. Preheating & Controlled Welding Techniques
Preheating before welding reduces thermal gradients and minimizes residual stresses.
Low-hydrogen welding electrodes can prevent hydrogen cracking.
Interpass temperature control reduces thermal stresses during multi-pass welding.
Narrow-gap welding reduces overall heat input and minimizes residual stress zones.
2. Selection of Low PWHT-Sensitive Materials
Some high-strength, low-alloy (HSLA) steels are engineered to resist hydrogen cracking and may not require PWHT.
Stainless steels and non-ferrous alloys often do not require PWHT due to their inherent properties.
Certain modern filler metals are designed to produce welds with lower residual stress.
3. Alternative Heat Treatment Processes
Induction heating can be used for localized stress relief in critical areas.
Mechanical stress relief (MSR) involves applying controlled external loads to redistribute residual stresses.
Vibratory stress relief (VSR) is used in some applications as an alternative to thermal stress relief.
Standards and Codes Governing PWHT Requirements
Various international standards regulate the necessity of PWHT for high-pressure components. Understanding these requirements helps in determining if PWHT can be avoided in specific cases.
1. ASME (American Society of Mechanical Engineers)
ASME Section VIII, Division 1 & 2 – Specifies mandatory PWHT for pressure vessels above a certain thickness.
ASME B31.3 – Covers PWHT requirements for process piping based on material type and service conditions.
Exemptions: Some materials under ASME codes may be exempt if they meet impact testing and hardness requirements.
2. API (American Petroleum Institute)
API 650 & API 1104 – Set guidelines for storage tanks and pipelines.
API RP 934-A – Defines alternative treatments for pressure vessels in refining applications.
3. AWS (American Welding Society)
AWS D1.1 – Structural welding code that allows exemptions based on material toughness and stress evaluation.
4. ISO & EN Standards
ISO 15614-1 & EN 13445 – Provide criteria for PWHT exemptions based on fracture mechanics testing.
Risks of Avoiding PWHT in High-Pressure Components:
If PWHT is skipped without proper analysis, several risks arise:
Increased likelihood of delayed cracking (due to residual stresses and hydrogen embrittlement).
Compromised mechanical properties leading to potential failure under cyclic loading.
Regulatory non-compliance if international codes mandate PWHT for specific applications.
Reduced corrosion resistance, particularly in high-temperature or aggressive chemical environments.
Conclusion: Can PWHT Be Avoided?
While there are scenarios where PWHT may not be mandatory, it requires strict adherence to material properties, alternative stress-relieving techniques, and compliance with international standards. Companies must conduct thorough assessments, including: ✅ Material & Weld Procedure Qualification Tests (WQT) ✅ Hardness & Impact Toughness Testing ✅ Residual Stress Analysis ✅ Regulatory Compliance Checks
At PWHT Tech India, we provide expert consultation and customized solutions for industries looking to optimize heat treatment processes while maintaining safety, durability, and compliance. If you’re considering alternatives to PWHT for high-pressure components, contact us today for expert guidance and evaluation.